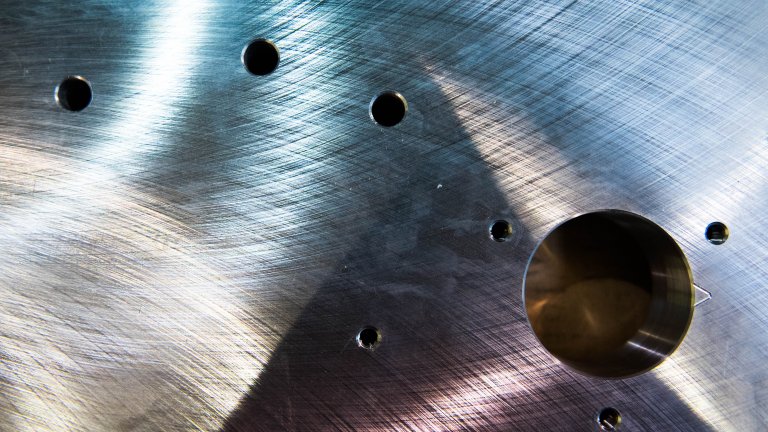
Special Coating Protects Stainless Steel from Fingerprints
The company Alutrim Europe GmbH from Kyritz is famous all around the world as a producer of surfaces and metal trims for cars and household appliances. The company from Kyritz is also advancing innovative developments in various areas. Research work is being conducted in eight different areas. One of its current projects: developing metallic surfaces that similarly to the display of smartphones respond to touch and can be used, for example, for adjusting the heating or locking the car door.
The coating must withstand extreme deformations of the material during the production process
Employees of the company have already worked for some time with extremely thin coatings that could make undesirable fingerprints on stainless steel a thing of the past. Especially producers of household appliances have pressed Alutrim again and again to apply these so-called anti-fingerprint coatings. The company is currently working on a research project with a projected runtime of one and a half years that is supposed to adapt these special coatings to the production processes at the company’s plant in Kyritz. “Stainless steel looks very exquisite, but it also has a disadvantage, namely that fingerprints are difficult to remove,” says Lutz Klinkner, Manager of Alutrim. “In the end it is always necessary to use a fat solvent to clean the surface effectively.” But there is an exception: metals covered in a nanometre-thick layer of anti-fingerprint coating, which can be described as a kind of special see-through organic-based coating. However, it would be too expensive to apply this coating to finished parts and so Alutrim has been working on a new production sequence since the end of 2015. The goal: applying the coating to the different raw material plates prior to their processing. The problem: the coating must withstand extreme deformations of the material during the production process.
Alutrim intends to use the coating for the widest possible array of applications
“Just imagine a flat Frisbee made out of metal that is being pressed into a narrow moulding form in order to shape it into a cooking pot,” says Klinkner. “The metal, of course, goes through a phase of extreme elongation.” This serves as a more or less fitting description of how Alutrim produces its parts through the process of deep-drawing and of what kind of deformations a coating would need to withstand without cracking. “We already have such a coating for aluminium,” said Klinkner and added: “but we still lack one for stainless steel.” It is Alutrim’s goal to make the coating available for the widest possible array of applications. To this end the company has constructed its own testing tools, which can produce considerable deformations. It is of special importance to find the right ingredients for the coating in order to make it as elastic as possible. So far it is not clear whether the process will really work. Klinkner thinks that the development process might have a 70% chance of succeeding.
The success story of the company Alutrim started in 2012. Back then new associates came to the company and Lutz Klinkner also became a manager. The plant in Kyritz joined the locations in Fuqing (China), Dayton (USA) as well as the newly established development location in Lindau (Bavaria) and became part of the “Alutrim Group”. Since then the company Alutrim Europe GmbH has nearly doubled its workforce: back then it had about 50 employees, today it has almost 100 and it continues to grow. “All of our business areas in Kyritz currently need new employees,” points out Klinkner.