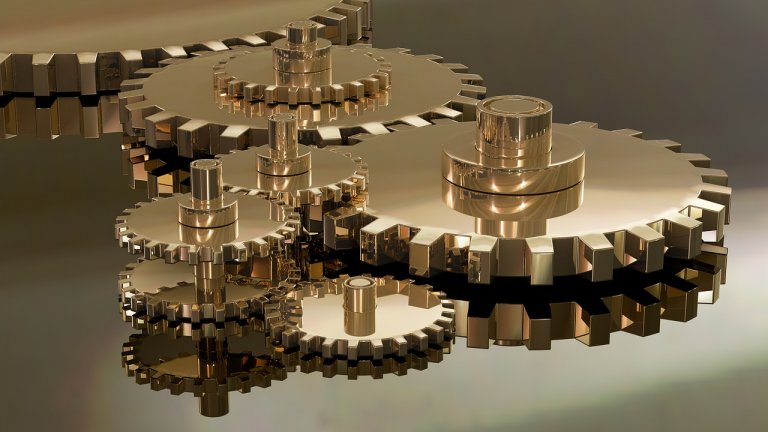
Surface Finishing Through Controlled Shot Peening
In the framework of the Fraunhofer innovation cluster “Life Cycle Engineering for Turbo Machines – LCE” a consortium consisting of companies and research institutes from Brandenburg and Berlin develops a process chain for the additive manufacturing of highly complex turbine components (project “ProFeX”). In this regard shot-peening is a technology of key importance for meeting the high quality standards of the industry and for seizing the full potential of additive manufacturing technologies.
Why controlled shot-peening?
In the area of additive technologies, selective laser melting has to be highlighted thanks to its versatility and application potential, mainly because it makes the manufacturing of complex, metallic components possible. Additive manufacturing components have a very coarse surface, which results from the process itself and poses a problem as it has a negative impact on the fatigue strength of the components. Controlled shot-peening can be used to make surfaces smooth and to significantly increase their fatigue strength.
In view of the often very complex geometry of additive components, the usual, mechanical surface processing methods, such as polishing, lathing or milling, are cumbersome because it is difficult to reach all the parts of the components. In this context, controlled shot-peening has a decisive advantage. The Metal Improvement Company (MIC), a subsidiary of the Curtiss Wright Corporation, offers controlled shot-peening services at its business location in Brandenburg; the services include the treatment of individual parts as well as of small- and large-scale series.
The company also boasts experience in other areas, for example, in the treatment of power plant components and chemical plants – ranging from newly-made products to repairs or maintenance. Thanks to MIC’s comprehensive experience in the field of aviation technology, mainly with regard to the treatment of engine components and turbo machines, the company brought vast expertise to the project.
The controlled shot-peening process
Controlled shot-peening is a cold working process during which the component’s surface is being shot-peened with round particles in a targeted manner; the particles’ material is optional and it can be metal, glass or ceramic. The particles’ high-energy impacts on the component surface cause plastic deformations as well as residual compressive stress near the surface.
The process creates dome-shaped structures near the surface, which, in turn, cause the surface area to expand. The inner layers of the material are trying to counter these expansions and plastic deformations near the surface. This accentuates the deformed material’s tendency to return to its initial form and leads to the creation of a layer near the surface of the cold deformed material with a –partially – high residual compressive stress. This residual compressive stress then leads to a considerably higher resilience of the surface vis-à-vis cracking, which increases the fatigue strength as well. This is especially important with regard to those parts of turbines that have to withstand high dynamic loads and that are of critical importance when it comes to safety; these parts form one of the focus areas of the project “ProFeX”. Furthermore, controlled shot-peening is being used for levelling the roughness peaks on the surface of components, which are created by the selective laser melting (SLM) method.
Objective
The properties of components produced through selective laser melting differ substantially from conventionally produced components. This posed a special challenge the company MIC had to face during its research on the influence of the shot-peening process on the fatigue strength and on the surface properties of turbine components made out of the nickel-based alloy Inconel 718, which have been produced through the selective laser melting (SLM) method. The research focused mainly on determining how the peening parameters are to be set in order to achieve optimal results with regard to roughness improvements. As to the fatigue strength, it was necessary to clarify what kind of improvements can be achieved and how the process influences the close contour areas of the components.
Approach
The SLM test specimens were produced at the Fraunhofer IPK. However, it is necessary to point out that first the company MIC substantially contributed to the project by providing support during the selection of the suitable geometrics for the subsequent assessment of the roughness, porosity, firmness and micro-structure. The company developed a comprehensive concept for the measurement and evaluation of these parameters. During the creation of the test matrix and the selection of the soon-to-be tested peening parameters, the MIC could rely on its long years of experience in the area of controlled shot-peening. Based on preliminary studies, the sizes of the shot-peening particles as well as their firmness and their cover ratio were determined through the suitable parameter space in the test matrix. This made it possible to unequivocally determine the influence of the individual parameters during the evaluation.
The evaluation of the treated surfaces included determining the influence the shot-peening particles’ type, their firmness and their intensity had on the material. The evaluation was followed by fatigue tests. Based on the results of the experiments conducted on the treated surfaces and based on the fatigue tests the optimal parameters were extracted from the test matrix.
Results and prospects
In the course of the project, a large number of studies have already been conducted on the test specimens and so a preliminary evaluation through the described study methods was possible. The studies demonstrated that the surface roughness of components produced through the SLM method can be significantly improved through controlled shot-peening. This improvement of the roughness ranks at 45 to 55% on the average. The studies have additionally shown that the firmness of the shot-peening particles accounts for impressive 10% of the roughness improvements and is therefore more important than the intensity of the shot-peening particles and their cover ratio, which account for about 7% and approximately 8% of the improvements respectively.
During the experiments, only the selection of the particles’ size played a minor role with regard to influencing the surface roughness as it accounted for only 3% of the improvements. As to the upcoming fatigue strength studies, it is already known that a too low intensity during the controlled shot-peening is unable to generate optimal firmness and that a too high intensity can have a firmness reducing effect within the component. One additional objective of the project, namely the creation of optimal surfaces while, at the same time, achieving the best possible fatigue strength properties, will therefore take centre stage during the upcoming studies. Based on the results of the fatigue strength studies, the best possible combination of parameters will be extracted from the test matrix. These parameters will then be used for creating a Woehler curve.
The Metal Improvement Company will continue to provide its knowledge and thereby important content for the upcoming material studies, which will focus on firmness analyses and on studies on the microstructure of the components. At the same time the company benefits from the close cooperation as it gains vital additional expertise in the field of additive manufacturing, which, in turn, strengthens Brandenburg as a business location.
The project was co-financed through funds from the European Regional Development Fund (ERDF)